For a long time, mold manufacturing has been a cornerstone of U.S. manufacturing. In the last few decades, this traditional process has evolved from the use of manual steel reeds to remove excess material, to the reliance on modern technology gas furnaces for the heat treatment of steel and the use of computer processing programs. Achieve perfect product quality and top production efficiency.
Fig. 1 Samples of parts cut from 6061 aluminum plates were machined by EDM machines and water jet cutting machines. Waterjet cutting machine tool saves 73% of the time compared to using EDM machine tools
Tools and molds of the 21st century can be divided into two major types: traditional and innovative. Each type can be determined based on its industrial application prospects. Traditional mold manufacturers belong to the older generation of tool and mold makers. They will focus on the application of manual technology to complete their mold manufacturing work. Innovative mold makers are a new generation of tool and mold makers. They will focus on the transformation of the entire process and rely on equipment and software to complete the task.
Now, the domestic mold industry is open to the global market, making this traditional business competition more cruel and fierce. The single biggest threat to the tool and mold industry is the obstruction of innovation. The growing business also includes adding automation equipment, adding programming software, streamlining processes, and introducing new technologies.
Figure 2 The domestic mold industry in the United States is open to the global market, making the competition in this traditional business more cruel and fierce
EDM Supplementary Technology
Water jet cutting technology is a complementary technology of EDM, and it has been increasingly accepted by people. For mold manufacturers, the processing speed of the water jet cutting machine tool is very ideal. It is suitable for rough machining and bulk material cutting before EDM finishing, which helps to shorten the production time.
In the mold manufacturing industry, EDM is a very common processing method. It is used in the machining of workpiece materials such as blind holes and cavities. EDM uses fuzzy logic technology, which can adapt to various minor changes in processing conditions, enabling workpieces to achieve micrometer surface quality. EDM processing technology has greatly improved the level of mold products, including product accuracy, quality, output and profits.
Figure 3 EDM processing technology is a very common processing method in the mold manufacturing industry
The ram-type EDM machine and EDM die-cutting machine are commonly used in the mold manufacturing process. This non-contact processing method combined with low-pressure flushing makes it possible to machine parts with very thin sections and high precision.
When machining a 1in (1in = 25.4mm) thick steel workpiece, we did a recent study comparing the cutting speed of the EDM WEDM with that of the water jet cutting technology. The test cutting of the EDM machine tool used a cutting line with a diameter of 0.012 in. As a result, the cutting speed was 0.25 in/min. Test cutting with a water jet cutter showed that the cutting speed can reach 2.9 in/min, which is more than 10 times higher than the cutting speed of the EDM cutter (see Table 1).
1. Theoretical basis
Water jet cutting is the use of high-pressure water flow, adding diamond abrasive in the water, and then high-speed jet to the workpiece to remove excess material on the workpiece. During water jet cutting, no heat is generated, so there is no risk of deforming the material. Because the excess material that is cut is blocky rather than swarf, materials can be saved, and excess material that is cut off can have other uses.
Roughing using a ram EDM or EDM wire cutting machine produces a heat-affected zone where the material generates high heat but does not melt. This high temperature zone will change the properties of the material. Therefore, the use of ram-type EDM machine for roughing is easy to produce high-energy heat, increase the risk of thermal deformation of the material, and affect the final quality of the workpiece.
In the water jet cutting process, when the water jets out from the small hole of the nozzle, the accuracy of the water flow will change, affecting the straightness and surface quality of the workpiece wall surface. Due to the fast processing speed of the water jet cutting technology, it is not guaranteed that the edge of the machining can reach the machining accuracy and tolerance size of the EDM machine tool. It is for this reason that these two processing technologies are seen as a complementary set of technologies.
Figure 4 Waterjet cutting machine tools are the most versatile cutting systems available on the market, creating tremendous wealth for moldmakers. In fact it can cut any material, including glass, ceramics, wood, stone, plastic and rubber, etc.
2. Benefits for the mold manufacturing industry
In particular, for mold manufacturers, where the time-consuming and less-accurate workpieces are required, the use of water-jet cutting technology is the best complement to EDM processing technology. For workpieces that require high tolerance dimensions and accuracy in the industry, EDM machines should be used for processing.
The application range of water jet cutting process far exceeds the basic application areas that people know. It brings speed and flexibility to EDM processing. We conducted another study on a 1 in. thick, 2 in. diameter part. The results show that roughing with water jet cutting saves 28% of the time compared to using an EDM machine (see Table 2).
3. Diversified production functions
For the mold industry, the diversified production of water jet cutting technology is no less important than its processing speed. In the United States, the company’s manufacturing operations cannot be guaranteed, depending on whether its domestic moldmakers can develop special processes or use specialized technologies that will help them survive. Water jet cutting technology allows moldmakers to separate from the narrow market and further expand their base customers.
Figure 5 Moldmakers should adopt new products and processes that are stimulating to the market
EDM processing technology is a specialized processing technology. It uses EDM methods to cut the workpiece, but it is only suitable for the processing of conductive materials such as graphite and metal. The waterjet cutting machine is a universal cutting system. It can cut a wide range of materials, such as glass, ceramics, wood, stone, plastic and rubber.
The edges of the parts machined by the water jet cutting technology are very smooth and bright, no sawtooth, metal slag or burr, no grinding or other finishing. Water jet cutting eliminates the need to replace tools or reposition the workpiece, saving time and money. Any part that does not require further processing by EDM machines in terms of tolerances, waterjet cutting techniques often require less than 10% of EDM processing time.
When purchasing a new set of equipment, one of the first things to consider is its ROI factor. For water jet cutting technology, as the speed increases, the average cost per inch of cutting will gradually decrease. Therefore, the machine can achieve maximum performance and profitability only at the optimum cutting speed. When the machine is operating at the highest power and speed as quickly as possible, the overall costs associated with cutting (including abrasives, power, water, filters, etc.) will be at a minimum. The application of water jet cutting technology in the mold processing workshop mainly lies in its cost. It is reflected in the workshop in the form of increased output and increased production capacity.
Moldmakers must continually seek new processing methods to further improve their production efficiency and capabilities. The application of new technologies such as water jet cutting will not only further increase the efficiency of mold makers, but its diversified production capabilities will stimulate the creation of new opportunities and open the door for new markets.
The design of middle through hole is easy to install, Barrel Damper is usually used in small spaces. ABD barrel dampers are the perfect solution for a wide range of applications. Barrel dampers are widely used in automobile interior decoration, household electric appliances, furniture, hidden socket, etc. Our dampers can make the movement of structures soft, quiet and safe to mitigate the impact, avoid the damage, increase the mechanical life, reduce noise, and improve product quality.
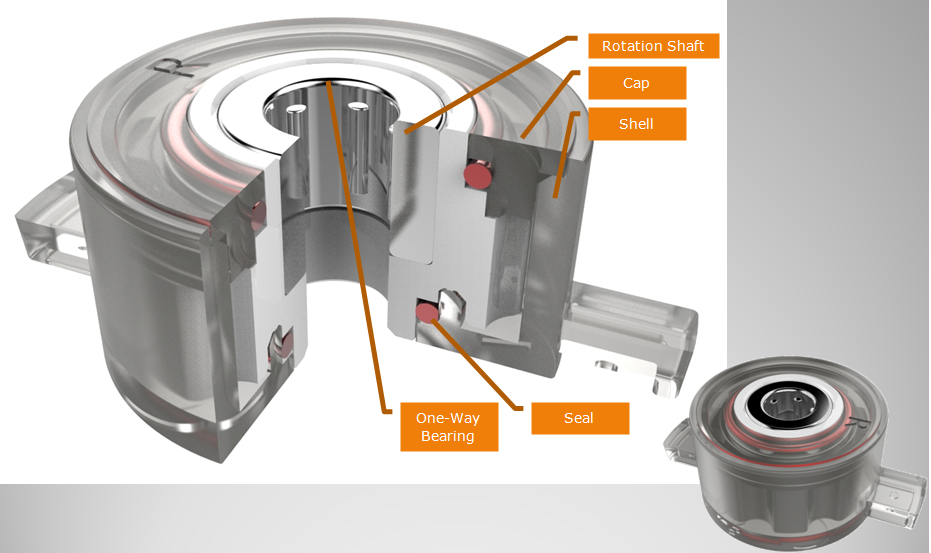
NOTE:
1. Please contact the corresponding product engineer for specific torque products.
2. Max. rotation speed: 50r/min
3. Max. circle rate: Clockwise180 °, 180 ° anti-clockwise for 1 cycle
4. Operating temperature: -10~50℃
5. Storage temperature:-30~60℃
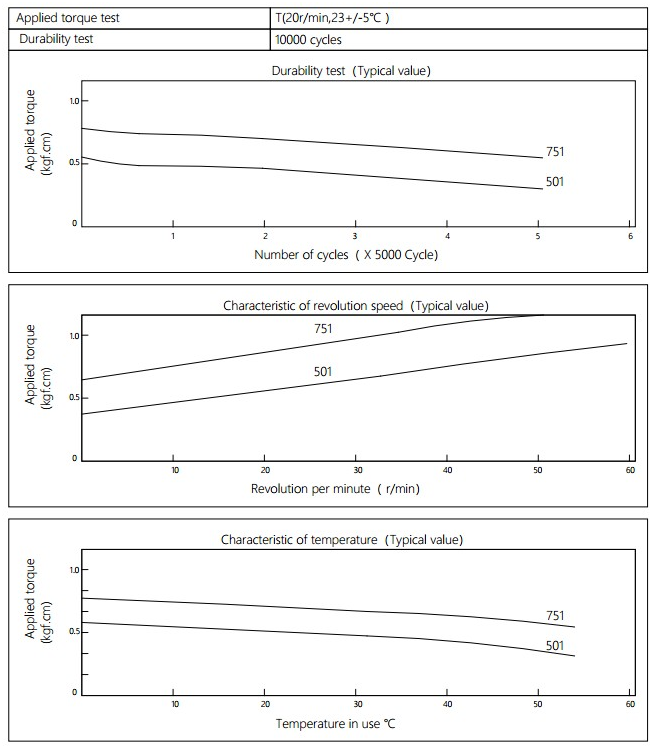
Applied torque:(T)
Test Temperature:23+/-5℃
Rotating speed:20r/min
Durability test Method:Clockwise 180 °, 180 ° anti-clockwise
Rotating speed:20r/min
Test Frequency:1cycle/min
Test Temperature:23±5℃
Durability test cycle:10000 cycle
Test result criteria: Store in the room temperature for 24 hours or more after the test, recording to the torque T=T±30%T.
Barrel Damper
Barrel Damper,Plastic Dampers,Manual Barrel Damper,Toilet Seat Damper,Plastic Barrel Rotary Damper
Shenzhen ABD Equipment Co., Ltd. , https://www.abddamper.com